Understanding Metal Turning Lathe Parts: The Backbone of Precision Engineering
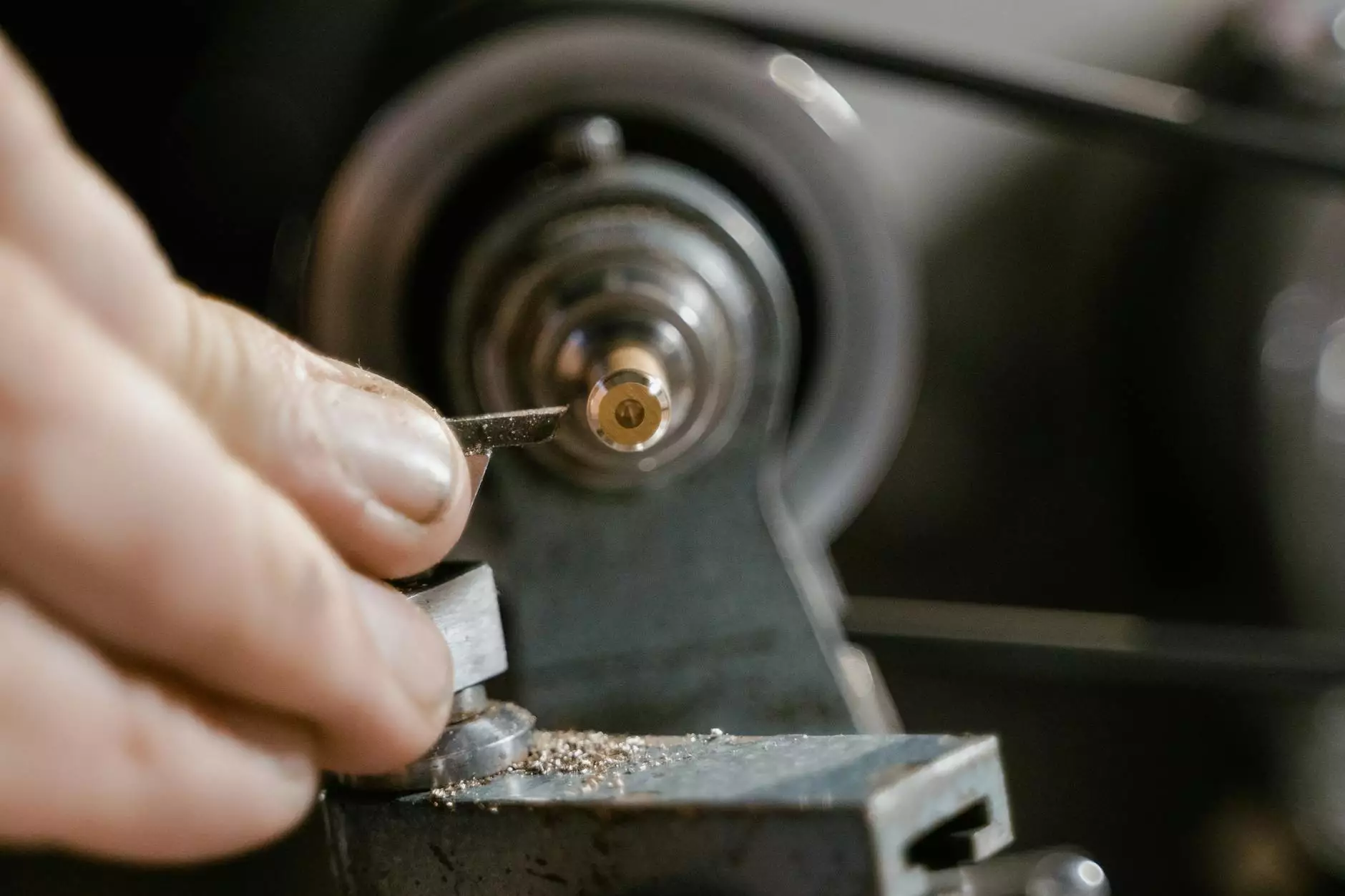
Metal turning lathe parts represent a critical component in manufacturing and machining industries. These indispensable parts are pivotal in the precision control and shaping of metal components, enabling a vast array of applications—from industrial machinery to automotive components. In this article, we will delve deep into the world of metal turning lathe parts, exploring their functions, applications, and why they are essential in modern manufacturing.
The Functionality of Metal Turning Lathes
A lathe is a versatile machine tool that rotates the workpiece against a cutting tool, allowing it to cut, shape, and finish materials. Specifically, metal turning lathe parts involve a range of components that ensure the lathe operates efficiently. Key parts include:
- Headstock: This is the part of the lathe that houses the primary drive mechanism, allowing the spindle to rotate the workpiece.
- Tailstock: Positioned opposite the headstock, it supports the workpiece and can be adjusted to hold different lengths.
- Carriage: This component holds and moves the cutting tool and is vital for achieving precise cuts.
- Tool Post: Part of the carriage, the tool post clamps the cutting tool securely in place while allowing for easy adjustments.
- Bed: The sturdy base of the lathe, the bed provides stability and support for all other components.
Importance of Precision in Metal Turning
In manufacturing, precision is non-negotiable. The ability of a lathe to create components that meet exact specifications is crucial in industries like aerospace, automotive, and electronics. Any deviation can lead to failures and increased costs. Metal turning lathe parts contribute to the precision of the lathe by:
- Ensuring uniformity: Each component has to meet specific standards to ensure the final product fits perfectly within an assembly.
- Minimizing tool wear: Quality lathe components reduce friction and wear on cutting tools, extending their lifespan and ensuring consistent performance.
- Facilitating fine adjustments: Many lathe parts allow for micro-adjustments, enabling machinists to achieve the utmost accuracy.
Applications of Metal Turning Lathe Parts
The applications of metal turning lathe parts are extensive and varied. They are used in numerous fields, including:
1. Aerospace Industry
In the aerospace sector, precision-engineered parts are critical. Metal turning lathe parts enable the manufacturing of lightweight yet strong components, such as turbine blades, shafts, and fittings.
2. Automotive Industry
Metal turning lathes are essential in producing components like crankshafts, gears, and brakes. These parts must meet high safety standards, making the role of lathe precision paramount.
3. Medical Devices
In the medical field, lathes are used to manufacture components of surgical instruments, prosthetics, and other critical devices. The precision of manufacturing ensures that these devices function reliably.
4. Electronics Manufacturing
Electronics require highly precise parts, such as connectors and housings. Metal turning lathe parts play a vital role in ensuring the performance and durability of these components.
Material Selection for Metal Turning Lathe Parts
The choice of material for metal turning lathe parts is crucial. Different materials offer varying benefits, such as strength, durability, and resistance to wear. Common materials include:
- Steel: Known for its robustness and versatility, steel is the most common material. Alloy steels enhance strength and toughness, making them suitable for high-stress applications.
- Aluminium: Lightweight and resistant to corrosion, aluminium is often used for components where weight savings are critical, such as in automotive and aerospace applications.
- Copper and Brass: These materials are prized for their excellent machinability and electrical conductivity, making them ideal for electrical components.
- Plastic Composites: In specific applications where weight savings and resistance to corrosion are essential, high-quality plastic composite materials are utilized.
Quality Assurance in Metal Turning
Quality assurance in the manufacturing process of metal turning lathe parts cannot be overstated. Ensuring that every part meets strict specifications involves several steps:
- Material Inspection: Before production, raw materials must be thoroughly inspected for quality, ensuring they meet industry standards.
- In-Process Inspection: Throughout the manufacturing process, periodic checks must be performed to ensure tolerances are maintained.
- Final Inspection: Every component undergoes a final inspection stage using precision measurement tools to verify that all specifications are met.
DeepMould.net: Your Trusted Partner in Metal Fabrication
At DeepMould.net, we understand the intricate nature of metal turning lathe parts. Our commitment to quality and precision ensures we provide exceptional components that meet the demands of modern manufacturing. Here’s why you should consider us for your metal fabrication needs:
- Expertise: With years of experience in the industry, our team possesses the knowledge and skills necessary to deliver premium quality parts.
- State-of-the-art Equipment: We utilize the latest technology to produce components with high precision, ensuring that every piece we manufacture meets rigorous standards.
- Customer-Centric Approach: We work closely with our clients to understand their specific needs, ensuring that we provide tailored solutions that fit their requirements.
- Competitive Pricing: Our pricing is designed to be competitive without compromising on quality, making us an attractive option for companies looking to optimize their budgets.
Future Trends in Metal Turning and Fabrication
The future of metal turning lathe parts and machining is evolving rapidly. Here are some trends to watch:
- Automation and Robotics: The integration of automation into machining processes helps increase production rates and reduce human error, leading to improved quality and reduced waste.
- Advanced Materials: The development of new materials, such as composites and advanced alloys, is opening new possibilities for lathe applications in various industries.
- 3D Printing: While traditionally not associated with lathe operations, 3D printing is gaining traction in producing complex components, which may lead to hybrid manufacturing processes.
- Smart Manufacturing: The rise of Industry 4.0 and smart factories, with interconnected machines capable of self-optimizing operations, represents a significant shift in the way lathe parts are produced.
Conclusion
In conclusion, metal turning lathe parts play an essential role in shaping the modern manufacturing landscape. Their contributions to precision engineering and applications across various industries cannot be overstated. Companies like DeepMould.net are at the forefront of this industry, offering unparalleled quality and service. As technology evolves, being informed about trends and innovations will empower businesses to remain competitive and efficient in their operations. If you’re looking for a reliable partner in metal fabrication, look no further than DeepMould.net; we are committed to your success.