The Benefits of Choosing a Leading Die Casting Manufacturer
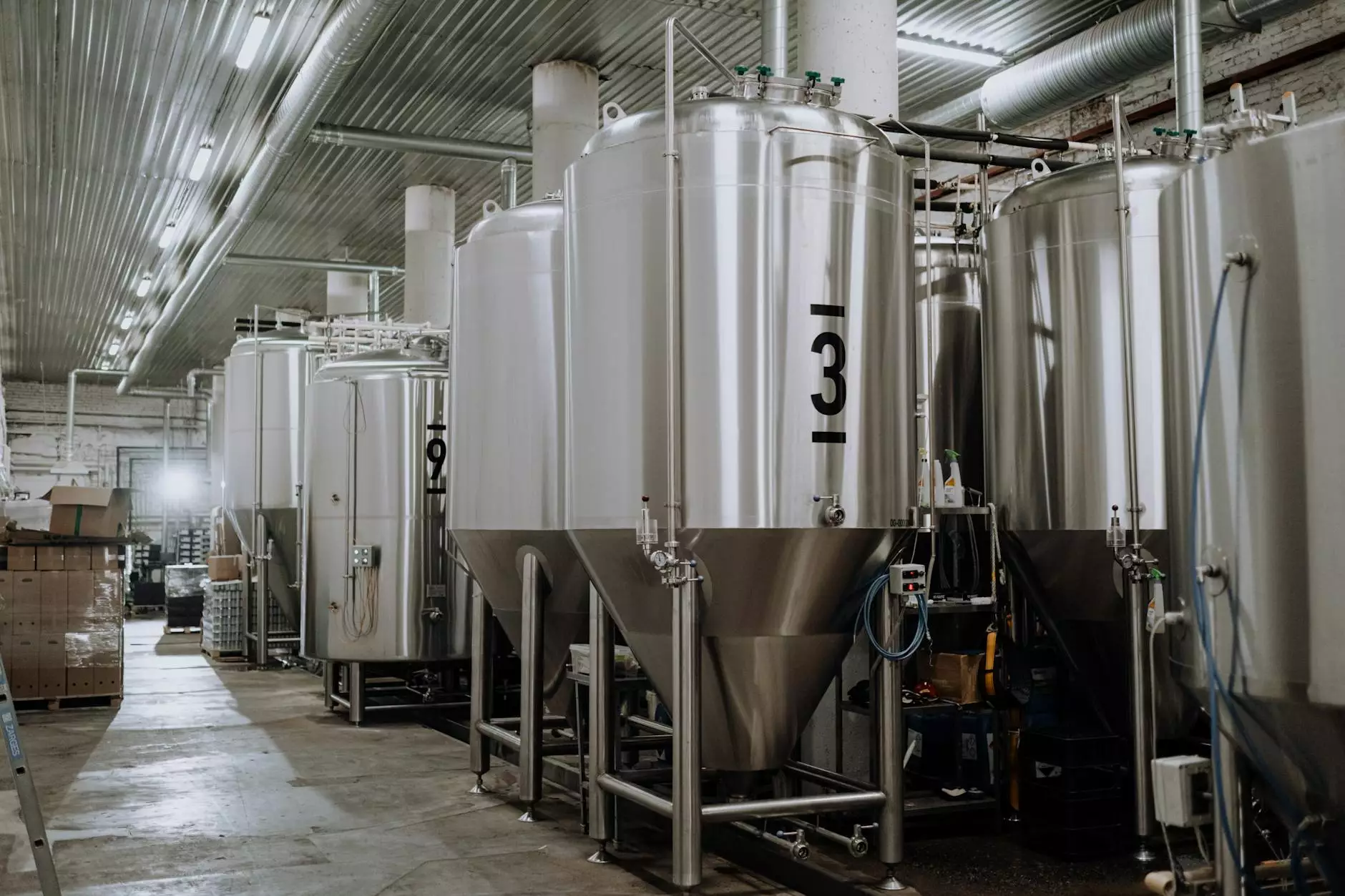
In today's highly competitive manufacturing landscape, selecting the right die casting manufacturer is critical for businesses aiming to produce high-quality metal components efficiently and cost-effectively. This article delves into the realm of die casting, analyzing its myriad advantages, industry applications, and the essential attributes to consider when choosing a manufacturer.
What is Die Casting?
Die casting is a metal fabrication process that involves forcing molten metal into a mold cavity under high pressure. This method is not only efficient but also allows for high-precision components with intricate designs. The die casting process is favored across various industries for its ability to produce large volumes of parts with excellent dimensional accuracy.
The Die Casting Process
The die casting process can be broken down into several key stages:
- Preparation: The first step involves preparing the metal, typically an alloy such as aluminum, zinc, or magnesium, which is melted in a furnace.
- Injection: The molten metal is injected into the die at high speed, filling the mold.
- Cooling: Once the mold is filled, the metal cools and solidifies, forming the final part.
- Ejection: The cooled part is then ejected from the mold using ejector pins.
- Trimming: Lastly, excess material is trimmed off, and the part is finished according to specifications.
Why Choose Die Casting?
Die casting presents a variety of benefits that make it an appealing option for manufacturers:
1. High Efficiency and Production Rates
One of the standout advantages of working with a die casting manufacturer is the ability to produce large quantities of high-quality parts quickly. The process allows for rapid cycle times, which can result in lower labor costs and higher output rates.
2. Exceptional Dimensional Accuracy
Die cast components are renowned for their excellent dimensional accuracy and consistency. This precision means that parts fit together seamlessly, reducing the need for extensive machining or adjustments.
3. Complex Geometries
Modern die casting techniques enable manufacturers to produce complex geometries that are often difficult or impossible to achieve with other methods. This capability opens up a world of design possibilities.
4. Excellent Surface Finish
Parts produced through die casting typically have a superior surface finish, which can reduce or eliminate the need for additional finishing processes. This results in both time and cost savings for manufacturers.
5. Material Versatility
Die casting can be performed with a range of alloys, including aluminum, zinc, and magnesium. Each material has its unique properties and benefits, allowing manufacturers to choose the best option for their specific application.
Applications of Die Casting
The versatility of die casting makes it suitable for a wide array of industries:
- Aerospace: Parts requiring high strength-to-weight ratios.
- Automotive: Components such as engine blocks, transmission cases, and decorative trim.
- Electronics: Housings and enclosures for electronic devices.
- Consumer Goods: Appliances and tools that require durable parts.
- Medical Devices: Components that must meet stringent safety and quality standards.
Choosing the Right Die Casting Manufacturer
Selecting a reliable die casting manufacturer is crucial to ensuring the quality and success of your production. Here are several factors to consider:
1. Experience and Expertise
Look for manufacturers with extensive experience in the die casting industry. Their expertise can significantly influence the quality and efficiency of the production process.
2. Quality Control Systems
A leading manufacturer will have robust quality control systems in place. They should comply with relevant industry standards and conduct regular inspections throughout the manufacturing process.
3. Technological Advancements
Innovative die casting manufacturers invest in the latest technology, such as robotic automation and advanced mold design software, to improve efficiency and quality.
4. Customization Capabilities
Different projects may have unique requirements. A good die casting manufacturer should provide customized solutions tailored to your specific needs.
5. Strong Customer Support
Effective communication and support are essential. A manufacturer that values customer relationships will be more proactive in addressing concerns and providing updates.
Environmental Considerations in Die Casting
In today’s environmentally conscious market, sustainability plays a vital role in manufacturing processes. Here’s how die casting can be aligned with green practices:
1. Recyclability of Materials
Many alloys used in die casting are highly recyclable, reducing the environmental impact associated with raw material extraction.
2. Energy Efficiency
Die casting often requires less energy than other metal casting processes, making it a more environmentally friendly option.
3. Reduced Waste
The precision of die casting means less material waste during the manufacturing process, which contributes to a smaller ecological footprint.
Future Trends in Die Casting
The die casting industry is constantly evolving, with several emerging trends that manufacturers and clients should keep an eye on:
1. Advanced Materials
Research into new alloys and composites is ongoing, aiming to enhance the performance characteristics of die cast components.
2. Automation and Smart Manufacturing
The integration of automation and smart technology is expected to enhance production efficiency and reduce costs in the die casting process.
3. Increased Demand for Lightweight Solutions
As industries lean toward lightweight components, mainly due to fuel efficiency and performance, die casting will play an increasingly important role.
Conclusion
Choosing the right die casting manufacturer can significantly influence the success of your production objectives. By understanding the benefits, applications, and factors to consider when selecting a manufacturer, businesses can make informed decisions that lead to high-quality, efficient, and sustainable production. As the industry continues to evolve, staying abreast of trends in technology and materials will ensure that your business remains competitive in an ever-changing marketplace.
For businesses seeking a trusted partner in die casting, Deepmould.net offers exceptional expertise and commitment to quality. Elevate your manufacturing with the advantages that only a leading die casting manufacturer can provide.