Understanding Prototype Molded Parts: A Comprehensive Guide
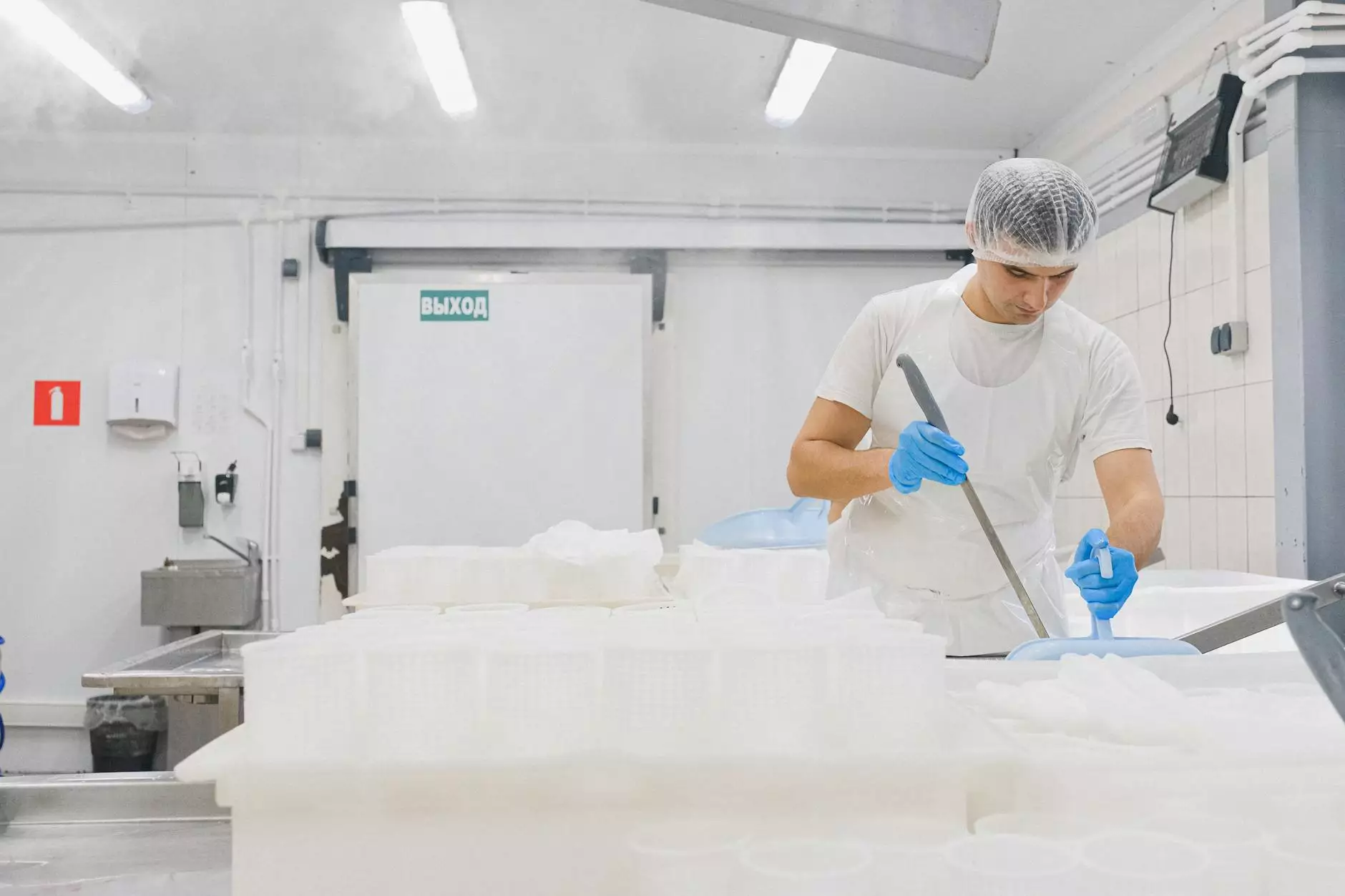
In the ever-evolving landscape of manufacturing and product design, prototype molded parts play a crucial role in translating innovative ideas into tangible products. These components are essential across various industries, including automotive, aerospace, consumer goods, and more. This article aims to provide an in-depth understanding of prototype molded parts, their creation process, benefits, and the significance of choosing the right manufacturing partner, such as the experts at deepmould.net.
1. What Are Prototype Molded Parts?
Prototype molded parts are initial versions of products created to test form, fit, and function before moving into full-scale production. These parts can be made from various materials, including plastic, metal, and composites, and they serve as tangible representations of a designer's concepts. The term 'prototype' indicates that these parts are not final products; instead, they are meant for evaluation, testing, and modifications, allowing for crucial feedback during the design phase.
2. The Importance of Prototype Molded Parts
The importance of prototype molded parts cannot be overstated. Here are several reasons why they are essential:
- Validation of Design: Prototypes help in validating design concepts and assumptions, ensuring that the final product meets the intended specifications.
- Cost Efficiency: By identifying design flaws early in the process through prototyping, companies can save significant amounts of money that would otherwise be spent on large production runs of flawed products.
- Market Testing: Prototypes allow companies to test market responses and gather consumer feedback before investing in mass production.
- Improved Communication: Having a physical prototype helps communicate ideas among engineers, designers, and stakeholders, facilitating collaboration and clarity.
3. The Process of Creating Prototype Molded Parts
Creating prototype molded parts involves several stages, each of which is crucial to ensuring the success of the prototype. Here's a detailed breakdown of the process:
3.1. Design and CAD Modeling
The first step in creating a prototype is developing a detailed design, usually with the help of Computer-Aided Design (CAD) software. This phase includes defining the dimensions, materials, and functionalities of the part. Designers must consider factors such as production methods, tolerances, and assembly processes during this stage.
3.2. Material Selection
Choosing the right material is vital for the success of prototype molded parts. Depending on the intended application, materials can range from thermoplastics to metals. Considerations include:
- Mechanical Properties: Strength, flexibility, and durability are paramount.
- Aesthetics: The looks of the prototype can influence market testing.
- Cost: Material costs can impact overall project budgets.
3.3. Production Techniques
Several production techniques can be employed to create prototype molded parts, including:
- Injection Molding: Ideal for high-volume production, but can be costly for low-volume prototypes due to mold-making requirements.
- 3D Printing: A rapidly growing method that allows for quick iterations and complex geometries, making it perfect for prototypes.
- CNC Machining: Offers high precision and can work with a variety of materials, often used for metal prototypes.
3.4. Testing and Iteration
Once the prototype is produced, thorough testing is conducted to evaluate its performance against the original design specifications. Feedback obtained from testing can lead to modifications of the prototype, and additional iterations may be necessary to refine the product further.
4. Benefits of Using Prototype Molded Parts
Utilizing prototype molded parts in product development provides numerous advantages, including:
4.1. Risk Mitigation
Prototyping helps identify potential issues before full-scale production. As a result, businesses can address concerns promptly, minimizing the risk of product failures and recalls.
4.2. Time Savings
Using prototypes speeds up the design process significantly. Rapid prototyping techniques enable teams to quickly iterate and test designs, leading to faster turnarounds.
4.3. Enhanced Customer Satisfaction
By testing and refining prototypes based on user feedback, companies can create more user-friendly products that meet or exceed customer expectations.
5. Selecting the Right Manufacturing Partner for Prototype Molded Parts
Choosing the right manufacturing partner can make all the difference in your prototyping success. Here are some essential criteria to consider when selecting a partner like deepmould.net:
5.1. Expertise and Experience
Look for a company with a proven track record in producing prototype molded parts. Their expertise in various manufacturing processes and materials will be integral to your project's success.
5.2. Technology and Equipment
Make sure the company invests in the latest technology and equipment. Advanced manufacturing techniques such as 3D printing, CNC machining, and high-precision injection molding are vital for producing high-quality prototypes.
5.3. Communication and Support
Effective communication is key throughout the prototyping process. Seek a partner who offers comprehensive support and keeps you informed at every stage, from design to production.
5.4. Flexibility and Scalability
Your chosen partner should be capable of adjusting production processes as your needs evolve. They should also have the capacity to scale up production if your prototype meets market demands successfully.
6. Conclusion
In conclusion, prototype molded parts are an invaluable asset in the product development lifecycle, enabling businesses to refine designs, enhance functionality, and reduce costs. By understanding the importance of prototyping and carefully selecting a manufacturing partner like deepmould.net, companies can innovate faster, meet customer needs more effectively, and ultimately achieve greater success in the marketplace.
Embracing the prototyping process not only leads to better products but also fosters a culture of continuous improvement and innovation, essential for thriving in today’s competitive landscape. If you're considering taking the next step in your product development journey, think about the significant advantages that well-executed prototype molded parts can bring to your organization.