The Crucial Role of Plastic Injection Molding Manufacturers
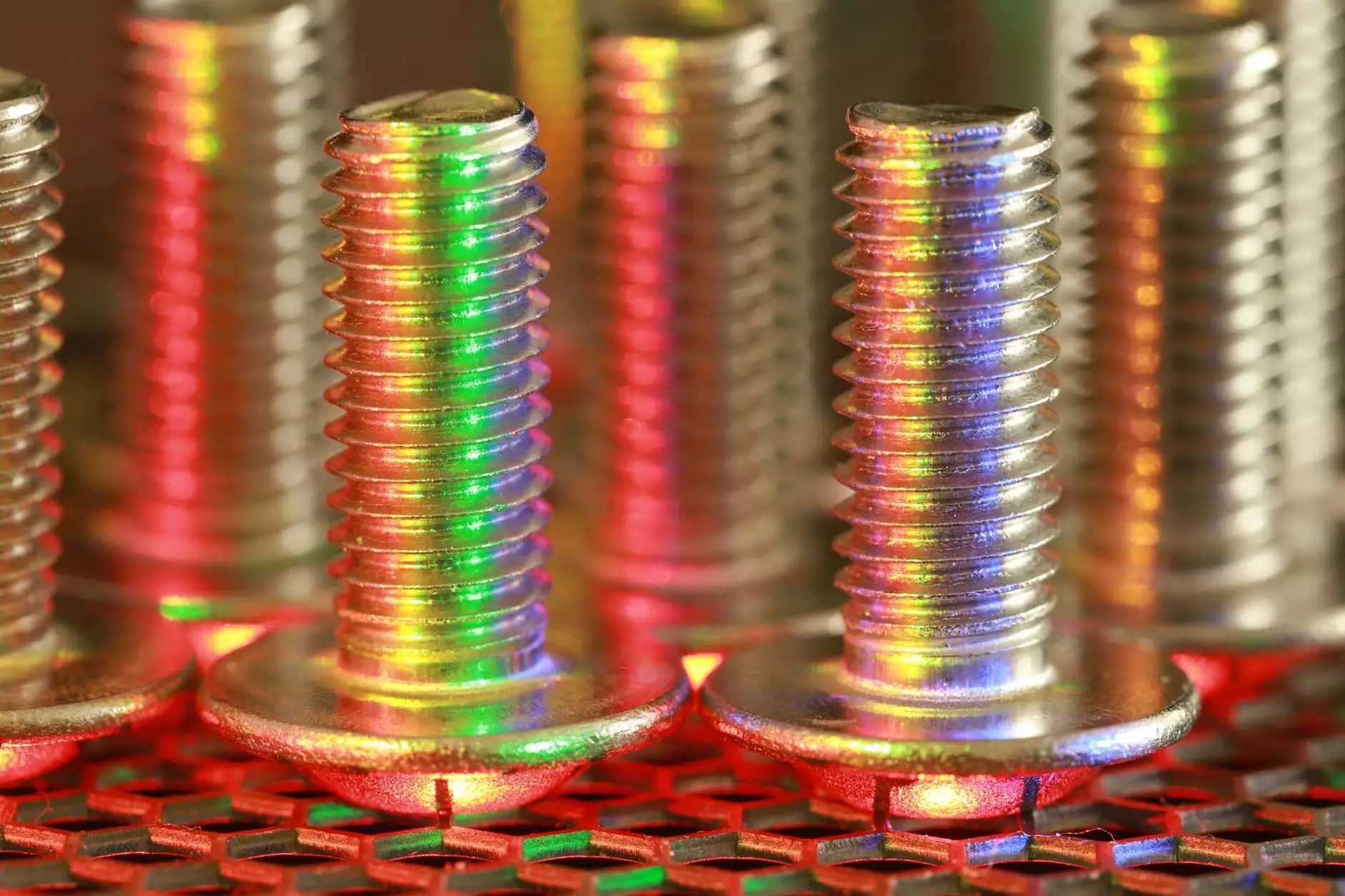
In today's rapidly evolving industrial landscape, plastic injection molding manufacturers play a pivotal role in the creation of products that touch nearly every aspect of our daily lives. This comprehensive article delves into the intricate world of plastic injection molding, offering insights into its processes, advantages, and the myriad applications that highlight its significance.
What is Plastic Injection Molding?
Plastic injection molding is a manufacturing process used to create parts by injecting molten material into a mold. This method is used for producing items in large volumes, offering superior efficiency and precision. The resultant products exhibit high strength and durability, making them ideal for various applications across multiple industries.
History of Plastic Injection Molding
The origins of plastic injection molding trace back to the early 1870s, when John Wesley Hyatt patented the process for creating billiard balls from celluloid. Since those early days, the technology has evolved dramatically, transitioning to a multitude of materials and applications, ultimately establishing itself as a cornerstone of modern manufacturing.
Advantages of Using Plastic Injection Molding
- High Efficiency: The injection molding process can produce large quantities of products in a relatively short amount of time, significantly reducing production costs.
- Design Flexibility: Manufacturers have the opportunity to create complex shapes that would be difficult or impossible to achieve using other manufacturing methods.
- Consistent Quality: The automation of the injection molding process allows for consistent manufacturing standards, reducing the risk of human error.
- Material Variety: A wide range of materials can be used, including thermoplastics, thermosetting polymers, and elastomers, allowing for tailored product development.
Understanding the Injection Molding Process
The plastic injection molding process involves several key steps:
- Material Selection: The appropriate type of plastic is chosen based on desired properties such as strength, flexibility, and temperature resistance.
- Melting the Plastic: The selected plastic is heated until it becomes a molten form, ready for injection.
- Injection into the Mold: The molten plastic is injected into a pre-formed mold that dictates the shape of the final product.
- Cooling: The plastic is allowed to cool and solidify within the mold.
- Demolding: After cooling, the mold is opened, and the final part is removed, completing the manufacturing cycle.
Applications of Plastic Injection Molding
Plastic injection molding is utilized across industries, addressing diverse needs:
1. Automotive Industry
The automotive sector relies heavily on plastic injection molding for components such as dashboard panels, interior fittings, and exterior body parts, due to plastic’s lightweight and durable nature.
2. Consumer Goods
From household appliances to toys, the consumer goods industry benefits from injection-molded plastics to produce durable, ergonomic, and aesthetically pleasing products.
3. Medical Devices
In healthcare, manufacturers create intricate parts for medical devices including syringes, surgical instruments, and diagnostic equipment which require high precision and stringent regulatory compliance.
4. Electronics
The electronics sector uses injection molding for producing enclosures, connectors, and various components, enhancing both functionality and appearance.
Choosing the Right Plastic Injection Molding Manufacturer
Selecting the right plastic injection molding manufacturer is crucial for the success of your project. Here are key factors to consider:
1. Experience and Reputation
Consider manufacturers with a proven track record and robust reputation in the industry. Reviews and testimonials can provide insights into their reliability and quality.
2. Technology and Equipment
Ensure that the manufacturer utilizes state-of-the-art technology and equipment. Advanced machinery can significantly affect the accuracy and speed of production.
3. Material Expertise
A deep understanding of different materials and their properties is essential. This expertise can help in selecting the right material for your specific application needs.
4. Prototyping Capabilities
Manufacturers that offer prototyping can help you visualize the final product and make necessary adjustments before committing to mass production.
Future of Plastic Injection Molding
The landscape of plastic injection molding continues to evolve with advancements in technology and sustainability. Innovations such as 3D printing and robotics are enhancing efficiency and precision, while increased focus on sustainability is driving the development of biodegradable and recycled plastics.
1. Sustainable Practices
Manufacturers are increasingly incorporating sustainable practices, using recycled materials, and optimizing processes to reduce waste and energy consumption.
2. Enhanced Technology
With the rise of smart factories, the integration of Artificial Intelligence (AI) and Internet of Things (IoT) technologies is streamlining operations and enhancing monitoring capabilities for better quality control.
Conclusion
In conclusion, plastic injection molding manufacturers are essential players in the modern manufacturing ecosystem. Their ability to produce high-quality, precise components efficiently makes them indispensable across various industries. As technology progresses and sustainability becomes more critical, the role of these manufacturers will continue to expand, driving innovation and shaping the future of manufacturing.
To explore more about the capabilities and offerings of a leading manufacturer in this space, visit Deep Mould, where innovation meets quality in plastic injection molding.