The Importance of Plastic Molding Tools in Modern Manufacturing
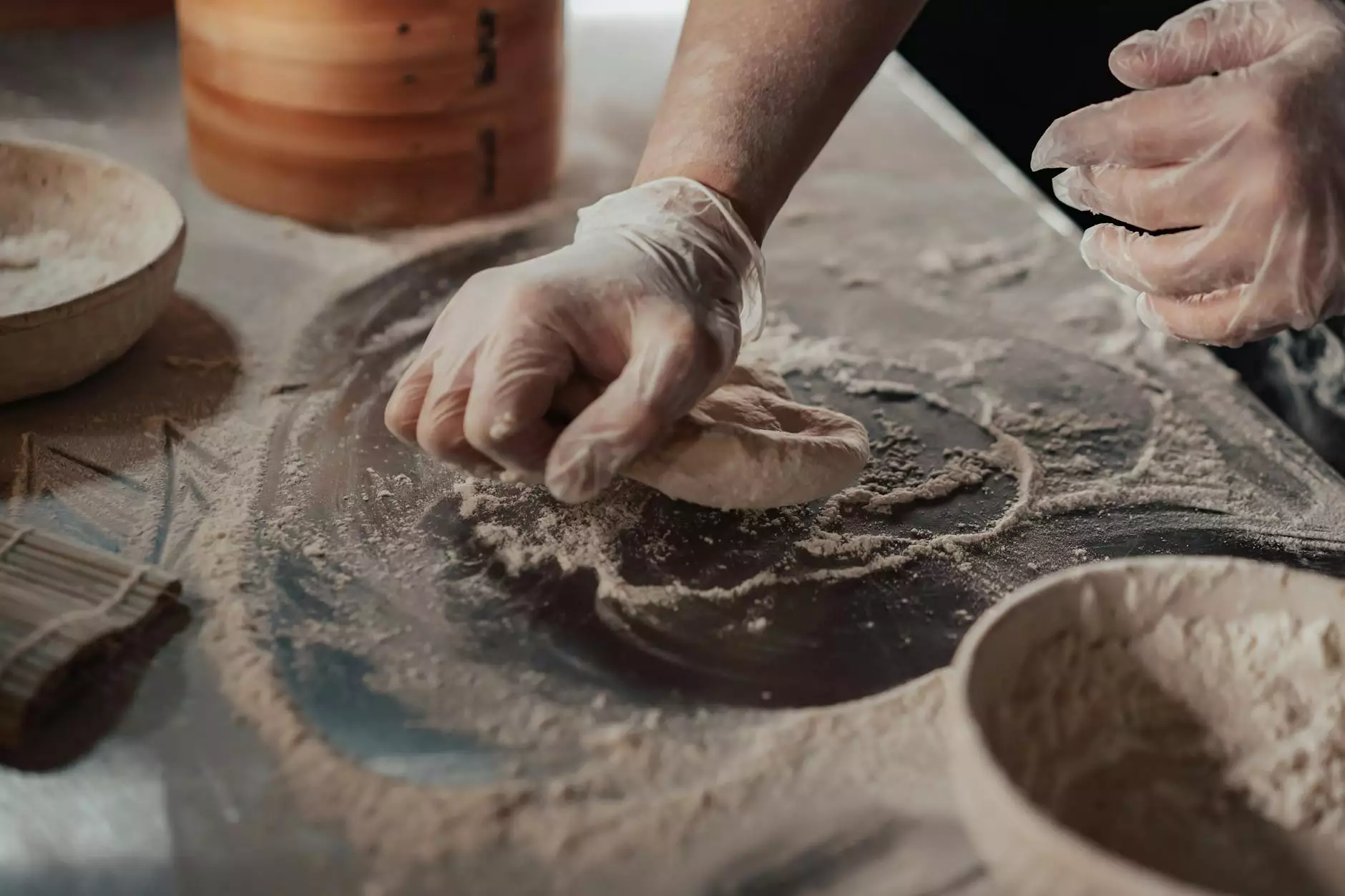
In the contemporary manufacturing landscape, few processes are as essential as plastic molding. The use of plastic molding tools has revolutionized the way products are manufactured, enabling businesses to create complex shapes with ease and efficiency. This article explores the intricacies of plastic molding tools, their applications, benefits, and the advancements that are reshaping the industry.
Understanding Plastic Molding
Plastic molding is a manufacturing process that involves shaping molten plastic into a desired form. This process begins with the heating of plastic materials until they reach a molten state. The molten plastic is then injected or compressed into a mold where it cools and solidifies into the final product. The effectiveness of this process heavily relies on the quality and design of the plastic molding tools used.
Types of Plastic Molding Tools
There are several types of plastic molding tools utilized in the industry, each serving a specific purpose. Here, we discuss the most common types:
- Injection Molds: Used for producing high volumes of parts with uniform dimensions, injection molds are one of the most widely used plastic molding tools.
- Blow Molds: Ideal for hollow products, blow molds are used to create containers such as bottles and drums.
- Compression Molds: These molds are used for thermosetting plastics and allow for mass production of detailed parts.
- Rotational Molds: Used for large, hollow products, rotational molds allow for even heat distribution and are perfect for complex geometries.
Why Plastic Molding Tools Matter
The significance of plastic molding tools in the manufacturing domain cannot be overstated. Here are some reasons why they are crucial:
1. Cost Efficiency
Using plastic molding tools can significantly reduce manufacturing costs. The ability to produce high volumes of plastic parts with minimal waste results in lower material costs. Additionally, the durability of these tools allows for longer production runs, which reduces the need for frequent replacements.
2. Precision and Quality
Modern plastic molding technologies allow for high precision in the manufacturing process. Plastic molding tools are designed to ensure that every molded part meets strict tolerances and specifications. This level of accuracy is vital for industries where part integrity is critical, such as automotive and aerospace manufacturing.
3. Versatility
Plastic molding tools can accommodate a wide range of plastic materials and complex designs, making them suitable for various industries. Whether creating simple components or intricate assemblies, these tools provide the flexibility manufacturers need to innovate and adapt to market demands.
4. Fast Production Rates
In today's fast-paced market, time-to-market is crucial. Plastic molding tools enable rapid production cycles, allowing companies to respond quickly to consumer demands and changes in the market. This speed is essential for maintaining a competitive edge.
Key Advancements in Plastic Molding Technology
The world of plastic molding is continuously evolving with technological advancements. Here are some key developments transforming the industry:
1. Automation and Robotics
Integrating automation and robotics into the plastic molding process has streamlined production. Automated systems reduce labor costs and improve consistency while enhancing safety by minimizing human intervention in hazardous environments.
2. 3D Printing for Tool Design
3D printing technology is now being utilized in designing and prototyping plastic molding tools. This allows for rapid prototyping and testing before mass production, significantly decreasing lead times and costs.
3. Advanced Materials
Innovation in material science has led to the development of new and improved plastics that offer better performance, durability, and sustainability. Advanced materials enable manufacturers to create stronger, lighter, and more environmentally friendly products.
4. Simulation and Computer-Aided Design (CAD)
The use of CAD software and simulation tools allows engineers and designers to visualize the molding process before production begins. This proactive approach reduces errors and optimizes mold design for better efficiency.
Applications of Plastic Molding Tools
Plastic molding tools are employed across various sectors due to their versatility. Here are some notable applications:
1. Automotive Industry
The automotive sector utilizes plastic molding tools for manufacturing components such as dashboards, bumpers, and internal parts, contributing to lighter vehicles and improved fuel efficiency.
2. Consumer Products
From household items to electronics, plastic molding is a cornerstone of product design, enabling the mass production of aesthetically diverse and functional consumer goods.
3. Medical Devices
In the medical field, precision and sterility are paramount. Plastic molding tools help fabricate medical devices and components, such as syringes and surgical instruments, ensuring quality and safety standards are met.
4. Packaging Solutions
Blow molds, in particular, are heavily utilized in the packaging industry to create plastic bottles and containers, ensuring products are safely stored and transported.
Choosing the Right Plastic Molding Tools
Selecting the appropriate plastic molding tools for your manufacturing needs can significantly impact the quality and cost-effectiveness of your production. Here are some factors to consider:
1. Material Compatibility
Different molds are suitable for various plastic materials. Ensure that your tools are compatible with the type of plastic you plan to use for your products.
2. Production Volume
Assess the expected production volume. For high-volume production, investing in more durable and advanced molds may be beneficial, while lower volumes may allow for simpler molds.
3. Complexity of Design
The design complexity of your product will dictate the type of mold tools required. Intricate designs may necessitate more advanced molding techniques and tools.
4. Budget Constraints
While high-quality molds can come with a significant initial investment, consider the long-term savings they may provide through efficiency and durability.
The Future of Plastic Molding
The future of plastic molding tools is promising, with continued innovation on the horizon. The industry is expected to embrace the principles of sustainability more rigorously, focusing on creating eco-friendly products and minimizing waste. Additionally, the integration of advanced technologies such as artificial intelligence and the Internet of Things (IoT) will further enhance production efficiency and quality control.
Conclusion
In conclusion, plastic molding tools play a vital role in modern manufacturing, offering myriad benefits including cost efficiency, precision, and versatility. As technology continues to advance, these tools will only become more integral to various industries, allowing businesses to innovate and meet the changing demands of the market. Investing in high-quality plastic molding tools is not just a necessity—it's a strategy for success in the competitive landscape of manufacturing.
At deepmould.net, we understand the importance of having the right plastic molding tools for your business. Our expertise and advanced capabilities in metal fabrication ensure that you receive nothing but the best in your manufacturing processes. Let's innovate together!